基本的な改善の進め方は、「開発・製造部門(直接部門)」も「営業・事務部門(間接部門)」も同様です。
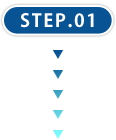
(何のために改善をするのか)
例えば | ・ 需要変動に強い企業体質にしたい |
---|---|
・ 生産性を向上したい | |
・ 残業を削減したい | |
・ 原価低減をしたい など… |
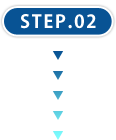
例えば | ① 課やラインを決める(これをモデルにして後々も他へ展開していく) ・ 直接部門では組立Aラインとする。 ・ 間接部門では管理部の生産管理課とする。 |
---|---|
② ○○事業部全体を対象にする | |
③ 全社的に同時展開する(製造部も管理部も営業部もすべて含める) など… |
例えば | ① 改善推進チームを決めて進める ・ リーダーとメンバーを決める。 ・ 組織内での改善推進チームの立場・権限を明確にしておく。 |
---|---|
② 各部・各課で部長あるいは課長をリーダーとして進める など… | |
③ 全社的に同時展開する(製造部も管理部も営業部もすべて含める) など… |
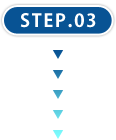
(何をどのくらい改善するか)
例えば | ① ○○の生産性を○○月までに○○%上げる |
---|---|
② ○○ライン(部署)のコストを○○月までに○○円下げる | |
③ ○○ライン(部署)の生産性を下げずに、○○月までに○○人減らし、 その人員を××部署に異動する。 |
|
④ 業務の処理時間を○○月までに○○分まで短縮する など… |
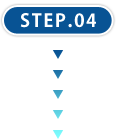
(整理・整頓・清掃・清潔・習慣)
- なぜ全員参加か・・・
- 全員が主人公(改善活動の当事者)という意識を持たせるため
- なぜ5Sから進めるか・・・
- ムダが体得できる。すぐに進められ効果もすぐ出るため
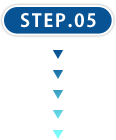
改善手法の実習・実践 : トヨタ方式の考え方
- 個別改善の実施
- 1ライン又は1部署の作業改善が中心
- 個別改善の実施(業務の見える化による改善)
- 1ライン又は1部署の作業改善が中心
①業務棚卸(G表)
②業務目的確認(S表)
③問題点・改善案抽出(F図)
④計画的実施(K表)
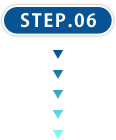
『あるべき姿』課題への解決とヒント
共に学び、共に考える
- 全体改善の実施
- 『あるべき姿』への実現を目指す
- 複数の工程・部署への改善(工程どうしのつなぎの改善)
- 原材料調達から出荷までのトータルな改善へ
- 全体改善の実施
- 『あるべき姿』を描きその実現を目指す
- 複数の部署にまたがるテーマの改善へ
製造会社では直接モノづくりに携わる、製造部門(加工ライン、組立ライン、検査ライン)が
これに当たる。
現場改善・生産リードタイム短縮・原価低減など(30社50事業所以上)
【国内】
株式会社紀文食品、化学薬品メーカー、建設部材メーカー、ガラスメーカー、
住宅建築メーカー、自動車部品メーカー、食品メーカー、その他製造メーカー様など
【海外】
韓国電気メーカー、米国木材加工メーカー、韓国食品メーカー、
インドネシア電気メーカー、中国電気メーカー様など
主に事務作業に携わる、管理部、営業部、総務部などがこれに当たる。
間接部門の改善・プライマリーバランスの黒字化(6団体260部門以上)
【国内】
岩手県庁、佐賀県庁、人材派遣業様など
【海外】
韓国電気メーカー様など